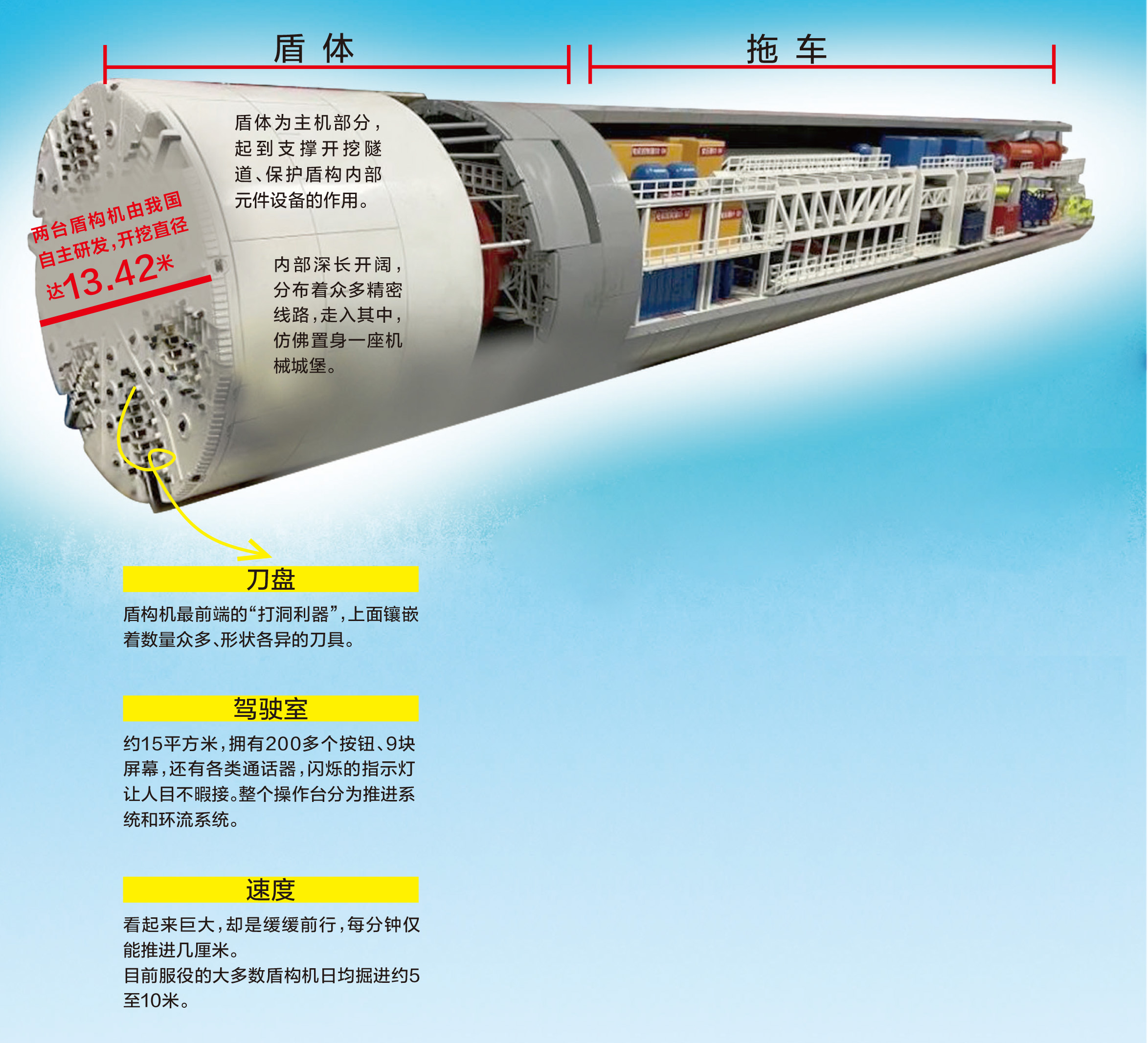
记者日前从中国铁建股份有限公司了解到,我国自主研发的海底隧道盾构机“深江一号”负责深江铁路珠江口隧道施工,目前已顺利掘进至海平面下100米深处。珠江口隧道为深江铁路重点控制工程,全长13.69公里,其中隧道盾构段最深处位于海底106米,是我国最深海底隧道。
据中铁十四局项目负责人李兵介绍,“‘深江一号’盾构机全线长距离下坡掘进,下穿珠江入海口,工程地质条件极其复杂。目前,盾构机已累计掘进3320米。”
珠江口隧道建设是我国地下空间开发利用的一个注脚。5月11日,中铁十四局“深江一号”盾构机模型亮相在上海开幕的2024年中国品牌日活动现场,吸引了不少参观者。
中国铁建地下空间开发品牌展区,通过全景式展现向观众科普中国地下空间开发核心技术。参观者通过裸眼3D,可看到盾构机犹如巨龙般在海底延伸;通过光影电梯,可深入正在地下搭建的“未来之城”,从36米到100米再到地下2400米,身临其境体验地下空间建造的神奇。
揭秘
穿越海底十几公里复杂地层 隧道最大埋深106米
由于深江铁路需要跨越珠江口狮子洋海域,地理环境十分复杂。设计人员经过数年方案比选,最终确定以隧道形式下穿珠江口。
珠江口隧道全长13.69公里,为单洞双线高速铁路隧道,隧道最大埋深106米,海水水压1.06兆帕,要穿越5种复合地质、13种地层、17条断裂带,全断面硬岩长2.75公里,是目前国内在建水下隧道施工难度最大的隧道之一。长距离穿越几十种复杂地层,这种难度的施工在全世界也属罕见。
量身定制两台国产盾构机 犹如巨型“穿山甲”
珠江口隧道工程位于东莞、广州之间的珠江入海口,2020年7月开工建设,为深江高铁先行开工段。
2021年投用的大直径盾构机“深江一号”采用醒狮造型涂装,“深江二号”采用蛟龙造型涂装,凸显广东地域文化特色。这台盾构机由我国自主研发,开挖直径达13.42米。两台盾构机从东莞虎门和广州南沙两端分别掘进。
“深江一号”总长130米,总重3800吨,由中铁十四局和中国铁建重工集团联合打造。“深江一号”穿越区间全长3590米,最大埋深106米,高水压施工区域110米,为目前国内埋深最大、水压最高的海底隧道。
重工业下的冷酷萌感让不少网友赞叹,“明明可以靠实力,却因为颜值强势出圈!”
总长133米、总重约3900吨的“蛟龙”绝对称得上是庞然大物。
盾构机这么重,应该是实心的吧?其实不然,盾构机内部深长开阔,分布着众多精密线路,走入其中,仿佛置身一座机械城堡。
由刀盘、盾体、拖车组成 刀盘为“打洞利器”
盾构机的结构有点像火车,由刀盘、盾体、配套拖车组成。“深江二号”共有5节,行走机构在最前面,后面一节节加挂。
刀盘为盾构机最前端的“打洞利器”,上面镶嵌着数量众多、形状各异的刀具。盾体为主机部分,起到支撑开挖隧道、保护盾构内部元件设备的作用。
据中铁十四局项目部负责人李兵介绍,隧道掘进过程中,盾构机需要在超高水压环境下进行海底换刀,对施工和设备性能要求极高。
研制团队在刀盘结构、刀具类型、驱动密封、盾壳设计、环流出渣、耐压耐腐蚀等各方面都进行了针对性研究与设计。
驾驶室约15平米有200多个按钮 每分钟仅掘进几厘米,日均5-10米
盾构机驾驶室约15平方米,拥有200多个按钮、9块屏幕,还有各类通话器,闪烁的指示灯让人目不暇接。整个操作台分为推进系统和环流系统。
由于土壤的软硬程度不均匀,盾构机挖着挖着容易发生偏移,这时候就需要人工来调整方向。
此外,盾构机长距离掘进后必须精准实现对接,犹如在大海中穿针引线,对盾构机掘进过程中的动态控制要求极为苛刻。
“95后”萌妹子杨涔是全国首位女盾构机司机,能操作如此精密的大国重器驰骋在百米深的海底,她感到十分自豪。
盾构机看起来巨大,却是缓缓前行,每分钟仅能推进几厘米。目前服役的大多数盾构机日均掘进约5至10米,而“深江二号”创下日掘进24米、单月最高纪录342米的好成绩。
延伸 国产盾构机逆袭
盾构机是目前最先进的隧道开挖装备,俗称“钢铁穿山甲”,集机、电、液、信息、人工智能等高技术于一身,具有数万个零部件。盾构机分两种,一种用于软土软岩隧道,另一种用于硬岩隧道,又名TBM(硬岩掘进机)。
“盾”,即“保护”,指盾壳;“构”,即“构筑”,指管片拼装。全世界的隧道工程,一半以上使用盾构机施工。
十几年前,国内盾构施工基本依赖进口设备,动辄数亿元的“天价”盾构机出现故障后只能停工,等待外国工程师维修。由于外方对技术实行垄断,维修保养时不允许中方参与,所需工时也完全取决于外方,严重影响工程进度。
2008年4月,我国研制出第一台拥有自主知识产权的复合式土压均衡盾构机,实现了从无到有的突破,并且在随后的几年里不断自主创新。中国最大直径土压平衡盾构机、中国最大直径硬岩盾构机、中国最大直径泥水平衡盾构机纷纷问世,自主研发的盾构机从“有”向“优”迈进。
从1995年,我国首次引进德国盾构机起,20多年来,自主创新的中国盾构机从蹒跚学步,到一路向前掘进,再到跨入世界先进行列,实现了完美逆袭。
如今,中国制造的盾构机技术过硬、物美价廉,逐渐反超欧美,占领全球大部分的盾构机市场。
截至2023年,中国盾构机在全球市场占比达70%。最新统计数据显示,截至目前,中国盾构机订单总数超过5000台,已出厂超过4500台,出口海外约40个国家和地区。
整合:易福红
采写:南都记者 钟丽婷
文/图来源:新华社 央视 人民日报等